3D 프린터의 등장으로 금속 절삭가공의 수요는 감소할 것이라는 설도 있었지만, 현재 그러한 경향은 그다지 보이지 않는다. 여전히 금속가공에서는 절삭가공이 많이 이용되고 있다. 단, 그러한 가운데 가공 및 가공기에 요구되는 요건은 변화하고 있다. 그 하나가 최근의 트렌드인 IoT 등의 인터넷 대응이고, 또 다른 하나가 기상 측정 시스템에 대한 것이다(그림 1).
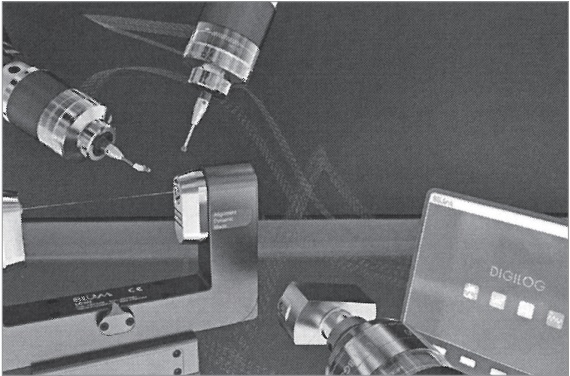
기상 측정 시스템
IoT 대응에 대해서는 주로 측정 결과를 외부 시스템으로 취득하고 싶다는 요구로, 측정 결과의 외부 출력 기능 자체는 예전부터 존재하고 있었지만 현재의 인프라 대응을 요구받고 있다. 예전에는 RS232C 경유로 외부 프린터나 PC로 출력하고 있었지만, 현재는 RS232C가 아니라 네트워크 경유로 데이터를 취득하는 사양으로 변화하고 있다. 그것이 공장 내뿐만 아니라 IoT 등의 흐름에 맞춰 인터넷 대응이 요구되고 있는 것이다.
다른 측면에서는 최근 가공 제품의 트레이서빌리티, 더 나아가서는 가공기의 트레이서빌리티 요구에 대응하기 위해 네트워크 경유의 데이터 취득 및 기록의 보관이 필요해지고 있다.
그러면 이야기를 기상 측정으로 되돌리면, 공작기계의 기상 측정은 대부분이 워크의 센터링, 공구의 길이 측정, 절손 검지에 이용되고 있다. 블룸노보테스트(주)에 문의하는 내용 중에는 가공 전의 레이저에 의한 공구 측정, 프로브에 의한 워크의 설치 상황을 측정해 센터링을 하는 것이 많다. 또한, 레이저에 의한 공구 측정, 프로브에 의한 측정 및 워크 원점 설정을 하는 것뿐만 아니라, 그 결과를 외부에 출력하는 것에 대해서도 문의를 자주 받는다.
최근에는 다른 목적으로 기상 측정의 수요가 증가하고 있다. 첫 번째 목적은 가공 정도의 향상이다. 이것은 최종 제품의 소형화, 고성능화를 위해 지금까지는 0.1밀리 정도로 충분했던 부품가공이 0.01밀리의 정도를 요구받기 때문에 프로브를 도입하는 케이스이다. 요구받는 정도에 대해서 블룸노보테스트(주)의 프로브는 반복 정도 0.2μm(TC52의 경우)를 자랑해 충분히 대응할 수 있지만, 유저가 프로브 도입에 주저하는 요인의 하나가 측정 프로그램이다.
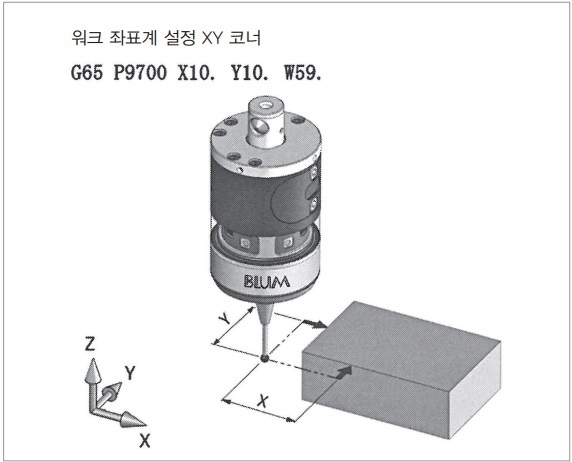
현재는 대부분의 공작기계 메이커가 터치 프로브의 하드웨어와 세트로 기본적인 기하 형상인 구멍, 원기둥, 입방체, 사각구멍, 기계축에 수직인 평면 측정을 하는 소프트웨어를 제공하고 있다. 이들 소프트웨어는 이전부터의 매크로 프로그램을 이용한 파라메트릭한 애플리케이션이다(그림 2). 이러한 애플리케이션은 터치 프로브 등장 시부터 현재에 이르기까지 주로 사용되고 있는 것이다. 이 애플리케이션은 오랜 기간 사용되어 신뢰성도 있고 좋은 제품이지만, 유감스럽게도 매크로 프로그램의 인수라는 파라미터 설정이 복잡하며 그렇기 때문에 멀리하는 사람이 있었던 것도 사실이다.
그래서 이 문제에 대응하기 위해 오늘날의 PC 기능을 갖춘 CNC에는 각사에서 GUI(그래피컬 유저 인터페이스)를 준비해 인터랙티브한 매뉴얼 겸 프로그램 작성 보조 툴을 제공하고 있으며, 블룸노보테스트(주)에서도 ‘Measure Xpert’를 출시하고 있다. 이것은 화면상에서 메뉴를 선택, 표시되는 안내에 따라 파라미터 설정함으로써 측정 매크로 호출 명령을 작성하고 CNC로 그 명령을 전송하는 일을 가능하게 한다. 이것은 블룸노보테스트(주)의 프로브 제품, 레이저 센서 모두에 대응한다. 현재는 FANUC제 iHMI 장착 CNC에 대응하고 있으며, 순차적으로 대응 기종을 추가해 갈 예정이다.
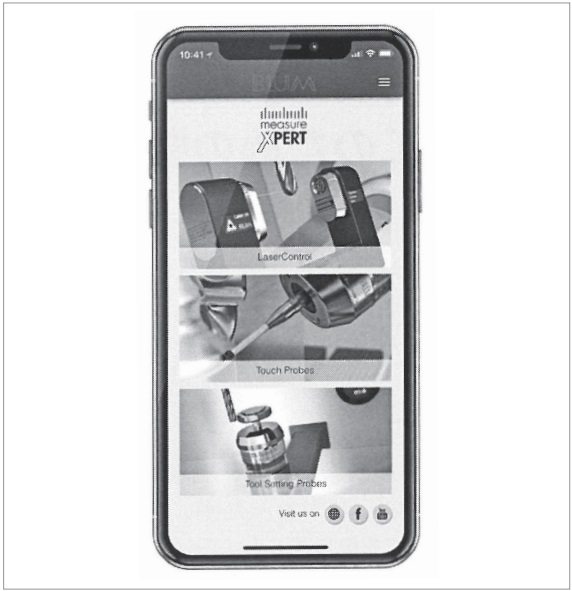
또한, 이 애플리케이션은 스마트폰판도 준비하고 있으며, 간편한 프로그램 작성 지원 툴로 활용할 수 있다(그림 3). 스마트폰판은 무료로 제공하고 있는데, CNC에 대한 데이터 전송은 대응하고 있지 않으므로 주의하기 바란다.
측정 데이터의 활용
측정 결과 데이터의 활용인데, 과거에는 RS232C 경유로 전용 프린터에 출력하는 전용 통신 소프트웨어를 사용해 퍼스널컴퓨터에서 수집하는 등의 이용 방법이 있었지만, 앞에서 말한 대로 현재는 RS232C가 아니라 네트워크 경유로 하는 것이 주류가 됐다. 블룸노보테스트(주)에서는 이 요구에 대응하기 위해 FANUC제 CNC 대응의 제품으로 ‘데이터 로거’라는 제품을 출시했다. 이것은 CNC의 매크로 변수에 보존된 측정 결과 등의 데이터를 네트워크 경유로 외부의 PC에서 수집하는 것이다. 작고 심플한 소프트웨어이지만, 유저에게 도움이 될 것으로 생각한다.
두 번째는 기기 외부의 측정기가 담당하고 있던 측정 프로세스를 공작기계 상에서 하는 ‘지금까지 공작기계 상에서 할 수 없었던 측정을 한다’는 것을 들 수 있다. 구멍이나 직방체 등의 단순 기하 형상이 아니라 금형, 터빈 블레이드 등의 자유곡면 측정에 대한 요구 등이 있다. 이 기능에 대해서는 앞에서 말한 매크로를 사용한 방법으로는 대응할 수 없다. 그것은 터치식 프로브의 특성 및 측정값의 보정 방법에 의한 것인데, 측정하는 면에 대해서 프로브가 법선 방향에서 터치해야 하고 자유곡면의 법선 데이터를 오퍼레이터가 하나하나 구해 프로그램하는 것은 현실적으로 불가능하다. 그렇기 때문에 그것을 실현하는 PC 소프트웨어 ‘Form Control’을 개발했다(그림 4).
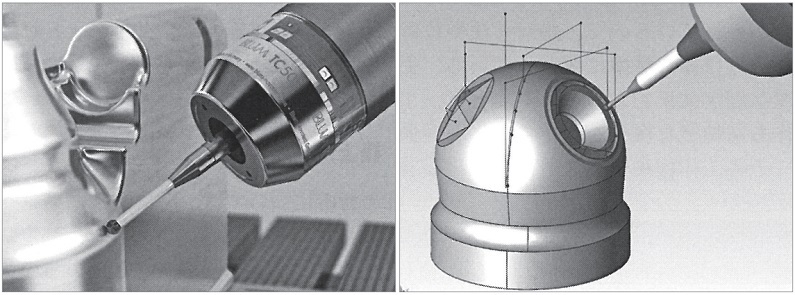
Form Control의 측정
Form Control은 측정 대상 형상의 CAD 모델을 사용, 측정하는 면의 법선 방향 정보를 얻는다. 그리고 CAD 상의 형상을 마스터로 해 실제 워크가 어느 정도의 오차를 가지고 있는지, 그것을 확인하기 위한 프로그램 작성, 데이터 수집, 데이터 처리, 오차 계산을 하는 것이다.
사용 방법은 간단하며, 측정 대상의 CAD 모델을 PC의 소프트웨어에 입력해 측정하고 싶은 포인트를 모델상에서 클릭한다. 지정된 포인트를 측정하는 프로그램이 생성되므로 그것을 NC에 로드해 실행한다(그림 5). 측정 결과는 FANUC CNC의 경우는 FOCUS 기능을 이용해 측정값을 Form Control이 인스톨된 PC에 넣는다. 데이터를 넣으면 데이터 처리, 오차 계산은 Form Control이 실행한다.
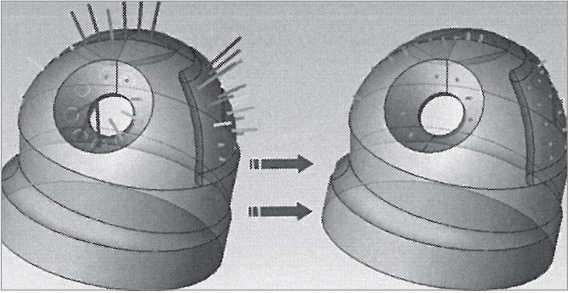
측정 결과의 표시는 CMM 유사 일람표 형식, CAD 모델상에 숫자를 표시, CAD 모델상에 색 구분해 표시 등의 옵션을 선택할 수 있다(그림 6).
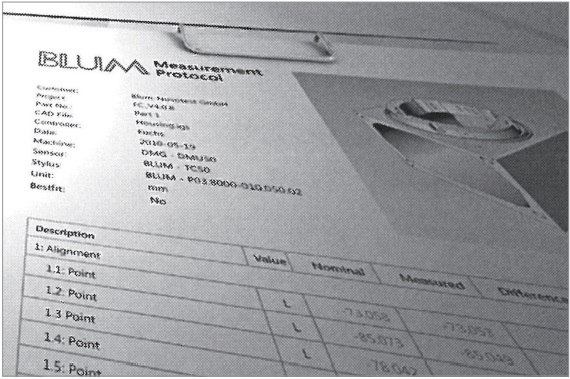
Form Control의 기능은 여기까지인데, 측정 포인트의 데이터를 텍스트 형식으로 출력할 수 있으므로 별도 CAD/CAM에 넣어 추입가공 프로그램을 작성하는 등의 이용 방법도 생각할 수 있다(그림 7).
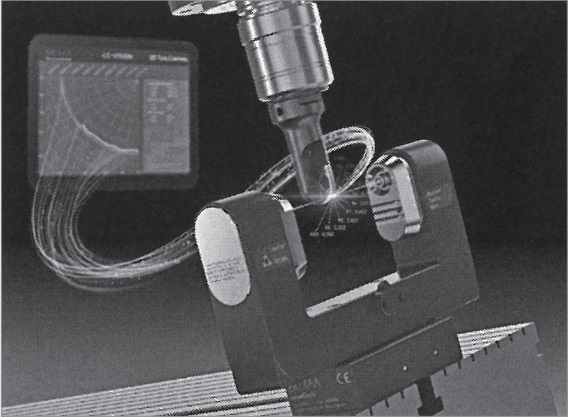
DIGILOG 측정
공구 측정에서 블룸노보테스트(주)는 C50-DIGILOG를 출시해 호평을 받고 있다(그림 8). 40년에 걸친 레이저 비접촉 공구 측정 기술을 개선해 하드웨어뿐만 아니라, 소프트웨어에 대해서도 크게 진보했다. 하드웨어 면에서는 레이저 소자, 광학 부품 등의 주요 기술 개량에 의한 정도 향상뿐만 아니라, 장치의 설치 공간이 되는 ‘스마트 독’ 내부에 에어 제어회로를 설치하고, 또한 스마트 독의 얼라이먼트 조정이 실시되어 있으면 레이저 센서 본체의 얼라이먼트 조정은 필요 없는 설계이기 때문에 메인티넌스 성능, 세트업의 용이성에 대해서도 크게 개선됐다(그림 9).
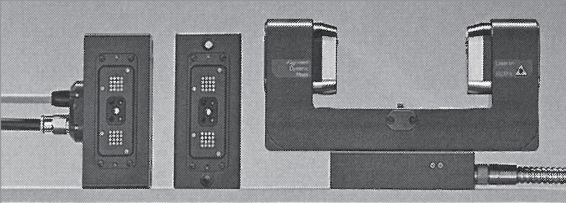
소프트웨어 면은 혁신적인 개량이 실시되어 기존의 레이저 센서 내부의 온·오프 두 가지 상태만으로 판단하고 있던 방법에 더해, 레이저 수광부의 아날로그 신호를 연속으로 받아들인 후에 디지털 처리하는 DIGILOG 방식에도 대응하고 있다(그림 10). 이것에는 두 가지 효과가 있는데, 하나는 레이저 센서의 약점이었던 ‘쿨런트나 절삭분 등에 의한 오검출’의 배제를 가능하게 한 점을 들 수 있다.
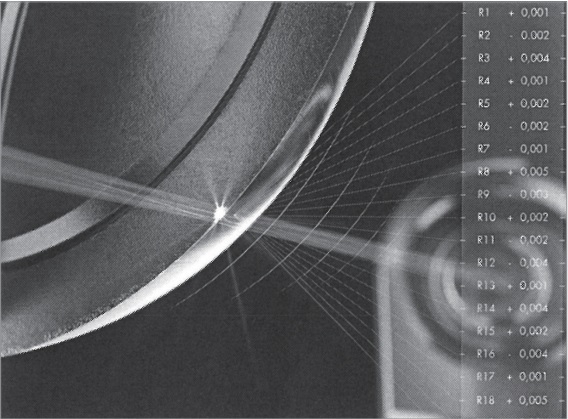
기존의 레이저 센서에서는 오신호인지, 본래 공구를 검출한 신호인지를 판별해 측정값의 신뢰성을 높이기 위해 여러 번 측정을 반복해 그 수치의 안정을 확인하는 기법을 사용했다. 그렇기 때문에 토털 측정 시간이 길어지게 된다. 그것에 대해 DIGILOG 방식에서는 한 번의 측정 동작 중에 센서 내부에서 레이저 센서의 수광량을 연속적으로 해석하기 때문에 기계의 움직임은 1회만으로 된다. 그 결과, 측정 시간의 대폭적인 단축을 실현하고 있다. 이 수광량은 공구가 회전했을 때에 절삭날에 의해 만들어지는 것으로, 연속적인 광량 변화의 데이터를 필터 처리한 후에 해석하고 거기에서 다양한 정보를 얻고 있다.
또한, 연속 데이터를 해석함으로써 각 절삭날의 지름·길이를 각각 파악할 수 있으므로 지금까지는 최대 지름·최대 길이밖에 파악할 수 없었던 공구 측정에 새로운 활용 방법을 제안하고 있다. 그것이 옵션 소프트웨어인 LC-Vision의 3D 툴 컨트롤이다(그림 11).
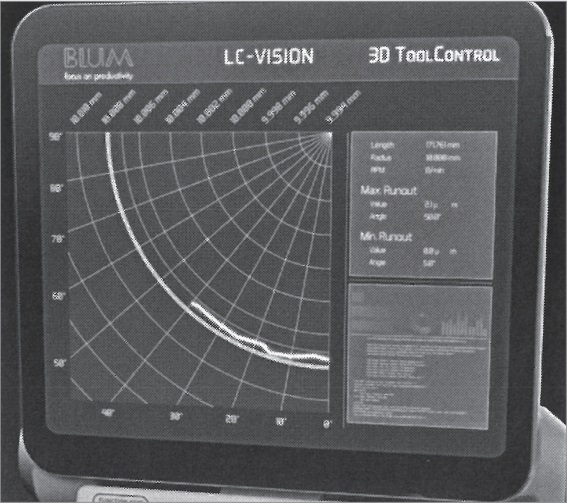
대상은 주로 볼 엔드밀이 되는데, 절삭날의 R 부분 각부의 치수를 측정하고 그 윤곽 형상을 플롯해 ‘어떤 부분이 가장 마모되어 있는지’, ‘R 형상에 근사시킨 경우, R의 치수는 얼마로 하면 좋은지’, ‘복수 날의 최대, 최소 치수’ 등의 계산, 그래픽 표시를 제공한다. 이 측정에서도 DIGILOG 측정이 위력을 발휘하고 있으며, 각 절삭날마다의 측정을 실현할 뿐만 아니라 측정 시간 단축에도 효과를 발휘하고 대량의 데이터 취득을 하는 애플리케이션도 비교적 단시간에 실행할 수 있다.
이와 같이 DIGILOG의 측정 메리트는 ‘측정 시에 연속 데이터 취득에 의한 신뢰성 향상’ 및 ‘사이클 타임의 단축’이라고 할 수 있다.
정밀 가공을 위한 기상 측정의 실현
그러면 이번 주제인 ‘정밀 가공을 위한 기상 측정의 실현’인데, 앞에서 말한 Form Control로 공작기계에서 워크를 내리지 않고 형상 측정 검증을 해서 그 데이터를 바탕으로 CAD/CAM으로 피드백을 하고 LC50 DIGILOG로 기상의 움직이는 상태의 공구를 정밀 측정한 공구의 치수를 설정함으로써 어느 정도까지의 정밀 가공은 실현할 수 있다.
그리고 이것을 실천하는 데 있어 다음의 세 가지 점에 유의하기 바란다. ①공작기계 자체의 정밀 관리를 확실히 할 것, ②공구를 기상에서 가공 시와 동일한 회전수로 측정할 것, ③측정 대상의 워크 및 공구를 적절하게 청소할 것이다.
프로브는 사용성이 좋은 측정장치이지만, 프로브 자체를 보증할 수 있는 것은 ‘반복 정도’뿐이다. 위치 정보나 치수값은 공작기계의 포지션 피드백에서 얻고 있으므로 절대 치수나 위치 정도는 공작기계 자체의 정도에 의존하고 있다. 따라서 고정도의 측정 결과를 요구받는 경우는 공작기계 본체도 고정도의 기계를 선정할 필요가 있다. 그리고 그 공작기계가 베스트 컨디션이 되도록 직각도, 진직도 등에 대해서는 충분히 조정한 후에, 열변위의 영향을 적극 배제하도록 적절한 난기운전을 실시하고 가공, 측정을 실시하기 바란다.
또한, 공구에 대해서도 마찬가지로 기상 측정, 가공 시와 동일한 환경의 측정값으로 확실하게 관리하기 바란다. 공구 측정은 공구를 회전시키면서 레이저로 측정하기 때문에 공작기계의 주축 특성이 반영된다. 가공 시의 상태에서 주축 특성도 포함해 측정하고, 가공에 반영시키기 위해 실제 가공과 동일한 회전수의 측정을 하도록 권장한다.
워크 측정, 공구 측정 모두 절삭분 부착에는 주의해야 한다. 워크 측정에서는 측정 프로그램을 연구해 측정값이 공차 외가 된 경우에는 재측정을 하는 등의 대책으로 오측정을 줄일 수 있다고 생각한다. 공구 측정, 특히 비접촉식의 공구 측정에서는 공구 표면에 대한 먼지 부착이나 쿨런트의 부착은 측정 결과에 크게 영향을 미치므로 공구의 클리닝을 활용하기 바란다.
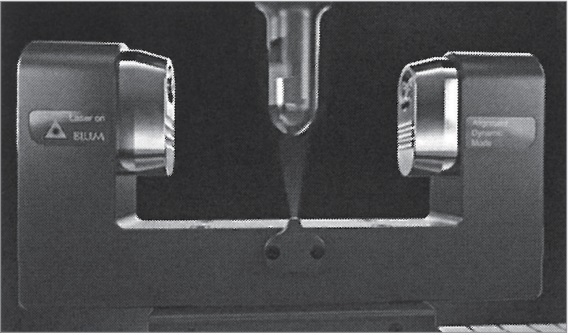
블룸노보테스트(주)에서는 NT 레이저에 옵션으로 공구 클리닝용 에어 블로 노즐을, LC50에서는 HPC(High Performance Cleaning) 노즐을 표준 장비하고 있는데, 이들을 충분히 활용해 공구 표면의 먼지뿐만 아니라 쿨런트를 충분히 제거하기 바란다(그림 12). 에어 블로 시간이나 어느 단계에서 에어 블로를 하는지 등은 동사 소프트웨어 내에서 조정할 수 있으므로 활용하기 바란다. 또한, 프로그램상에서는 쿨런트를 정지시켰지만, 실제로는 배관 내부에 남아있는 것이 계속 흐르는 경우도 있다. 그러한 경우는 공구 측정을 실시하기 전에 체류 시간을 설정하던가, 쿨런트 배관에 체크 밸브를 추가해 쿨런트의 흐름을 제어하도록 하면 안전하다.
맺음말
앞에서 ‘어느 정도까지의 정밀 가공’이라고 말한 것은 측정으로는 커버할 수 없는 요인이 있기 때문이다. 그것이 공작기계, 주축, 공구의 강성이다. 특히 공구에 대해서는 탄성 변형이나 절삭날 형상에 의한 릴리프, 식입이 발생하는 경우가 있다. 이러한 경향에 대해서 동사의 소프트웨어에서는 ‘추가 길이 보정’, ‘추가 반경 보정’ 등의 파라미터로 커버할 수 있게 되어 있으므로 활용하기 바란다. 이번에 소개한 측정장치․소프트웨어가 유저의 정밀 가공, 고정도 가공에 도움이 되기를 바란다.