국내 제조업 현장은 자동화와 디지털 전환의 필요성을 절감하고 있음에도 여전히 수기 작업과 단편적 시스템 운영에 의존하고 있다. 기계 가동률은 평균 80%에 달하지만, 실제 부가가치를 창출하는 생산 가동률은 30%에도 미치지 못한다. 근무 시간 중 약 6시간은 설비 대기, 원자재 탐색, 오류로 인한 중단 등 비가시적 손실로 낭비된다. 특히 숙련 인력의 고령화와 신규 인력 유입 감소가 이런 비효율을 심화시키고 있으며, 다품종 소량 생산과 빠른 납기를 요구하는 시장 변화에 기존 방식은 한계에 직면했다. 판금 가공, 레이저 절단, 절곡 등 정밀 가공 분야는 특히 연결성과 숙련도 의존도가 높아, 작은 비효율도 수익성에 큰 타격을 준다. 이에 따라 제조업계는 데이터 기반 의사결정과 지능형 자동화 시스템을 도입해 생산성을 극대화하고 지속 가능한 성장을 도모해야 할 시점이다.
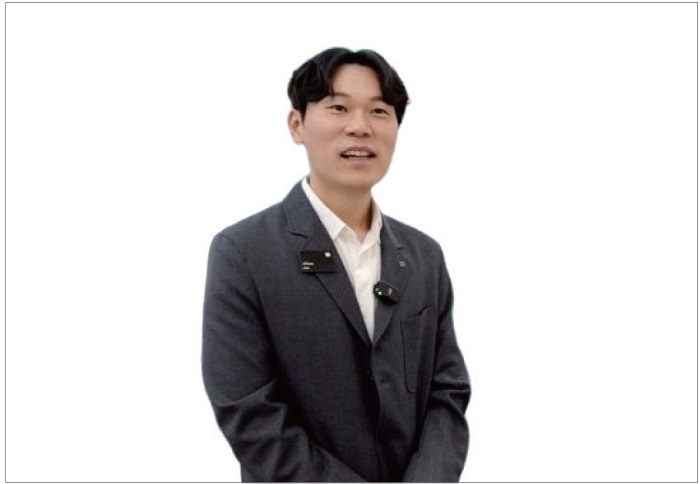
단일 장비 넘어 솔루션으로...TRUMPF, ‘종합설비효율’ 극대화 가속 겨냥
이러한 전반적인 제조업의 난관 속에서, 공작기계 산업은 생산의 핵심 동력으로서 더욱 고도화된 솔루션을 요구받고 있다. 기존 장비 대비 생산 공정 전체의 효율을 진단·최적화해, 현장 내 종합설비효율(OEE)를 극대화하는 통합적 접근 방식이 새로운 해법으로 부상하고 있다.
주지훈 한국TRUMPF 머신툴 사업부 기술 영업팀 프로는 “과거 공작기계 업계는 단순히 장비를 판매·설치하는 과정에 집중했다”며 “현시점에는 각 현장의 전반적인 제조 환경을 이해하고 숨겨진 비효율을 찾아내 해결하는 것을 목표로 한다”며 공작기계 생태계가 현재 제조업에 제시하는 핵심 인사이트를 강조했다.
글로벌 공작기계 솔루션 업체 TRUMPF는 앞선 시대적 요구에 발맞춰, 제조 현장의 비효율성을 진단하고 있다. 이에 대한 근본적인 해결책으로, OEE 극대화를 위한 통합 솔루션을 제시하고 나섰다. 이는 각 현장의 실질적인 생산 효율성을 끌어올리는 데 집중하겠다는 확고한 의지다.
TRUMPF는 그동안 판금 가공 및 레이저 기술 분야에서 다양한 경험을 축적했고, 이를 기반으로 다각적인 경쟁력을 갖추고 있다. 특히 금속 가공 산업에 특화된 2D 레이저 절단기를 지속 개발해 고도화 혁신을 달성하는 등 새로운 활로를 열고 있다.
TRUMPF의 주요 제품은 이처럼 첨단 레이저 기술을 기반으로 한다. 얇은 시트부터 두꺼운 판금까지 정밀 절단하는 ‘레이저 절단기’, 금속판에 다양한 형태의 구멍을 뚫고 레이저로 가공하는 ‘복합기’, 판재를 정교하게 절곡하는 ‘절곡기’, 파이프 레이저 절삭 가공이 가능한 ‘파이프 레이저’ 솔루션 등이 대표적이다.
특히 기계와 소프트웨어를 통합해 생산성을 높이는 데 집중하고 있다. 자동화 및 소프트웨어 역량을 강화해, 각종 현장의 스마트 팩토리 구현을 지원하고 있다.
사용자 중심 전략의 핵심 축 ‘재정의’하다...소프트웨어 기반 토털 솔루션 ‘앞장’
TRUMPF는 생산 효율 극대화를 위한 핵심 전략으로 하드웨어·소프트웨어의 유기적인 통합을 내세운다. 스마트 팩토리 통합 생산 관리 소프트웨어 ‘오션(OSEON)’이 대표적이다. 이는 사용자 인프라의 숨겨진 비효율을 진단·해결하고, OEE를 극대화하는 데 결정적인 역할을 한다.
OSEON은 크게 생산 관리, 현장 제조, 물류 관리, 분석 모듈로 구성돼 있다. 설계·절단·절곡·조립에 이르는 전반적인 생산 흐름을 디지털화한다. 이를 토대로 △공정을 실시간으로 제어하고 △작업 지시를 자동화하며 △자재 흐름을 추적하고 △장비 효율을 최적화한다.
주지훈 프로는 “생산 공정 및 자재 흐름의 투명성을 확보하고, 복잡한 현장 내 설비 효율과 생산성 정보를 빠르고 쉽게 파악할 수 있다”고 오션의 강점을 피력했다. 그에 따르면, 하드웨어만을 활용하면 눈에 보이는 생산 효율을 높이지만, 오션은 눈에 보이지 않는 장비 가공 전 비생산 시간까지 절약하며 OEE를 한층 끌어올릴 수 있다.
이러한 오션 소프트웨어는 얼마 전까지만 해도, 대규모 업체·현장에 적합하다는 인식이 강했다. TRUMPF는 이를 개선하기 위해 중소·중견업체까지 아우를 수 있도록 플랫폼을 진화시켰다. 이 과정에서 전사적자원관리(ERP) 시스템 부재로 인해 오션 도입을 주저한 업체를 위해, ERP 역량을 갖춘 파트너사와 협력해 중소·중견 맞춤형 ERP 프로그램을 개발했다.
이를 통해 자체 ERP가 없는 현장에서도 오션을 효율적으로 활용할 수 있는 토대가 마련됐다. 이는 OSEON 도입의 문턱을 낮추고, 기업이 DX의 혜택을 누릴 수 있도록 지원하는 중요한 계기가 됐다.
주 프로는 “오션은 생산 관리 툴 본연의 역할은 물론, 장비 작업자에게 실시간 작업 지시를 내리는 기능까지 수행한다”며 “이 밖에 컴퓨터지원설계(CAD)·디자인 데이터, 수주·단가·수량 등 비즈니스 데이터 등을 디지털화하는 역량도 함께 갖췄다”고 말했다. 그러면서 “모니터 하나로 모든 것이 통합 가능한 환경을 구축해, 과거 수기로 인한 인적 오류를 저감하고, 생산 효율성을 극대화하는 데 결정적 역할을 할 것”이라고 덧붙였다.
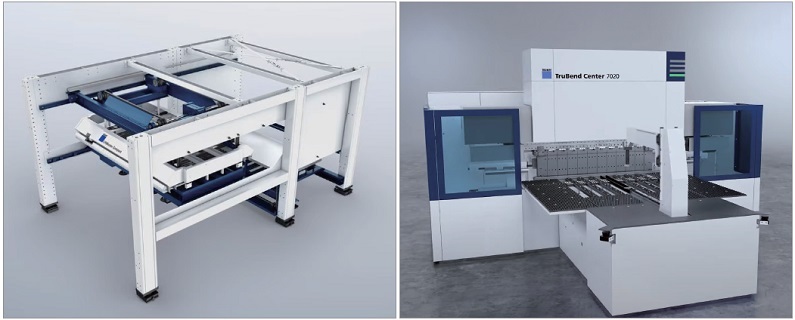
“숨겨진 비효율 잡아야 진정한 생산성” 하드웨어·서비스 결합으로 시너지 노린다
TRUMPF는 앞선 소프트웨어 솔루션과 더불어, 지능형 자동화를 통한 실제 생산 시간 확보에 주력한다. 이 비전은 장비의 가동 중단 시간을 최소화하고, 예기치 못한 고장을 방지해 실질적인 생산 시간을 늘리는 데 초점을 맞춘다.
하드웨어 측면에서는 자동 창고 시스템 ‘TruStore 3040’, 자동 로딩·언로딩 장비 ‘LiftMaster Compact’, 자동 패널 절곡기 ‘TruBend Center 7020’ 등을 핵심 축으로 내세운다.
특히 각 솔루션 간 융합을 통한 솔루션 제시를 차세대 비전으로 삼는다. 고성능 2차원(2D) 레이저 절단기 ‘TruLaser 5040 fiber’, Trustore 3040, LiftMaster Compact 등 세 장비의 결합이 대표적 솔루션 사례다.
이는 24시간 무인 생산 시스템을 가능하게 해, 현장의 비효율을 획기적으로 줄여줄 핵심 조합이다. 이 중 Trustore 3040은 콤팩트 설계로, 최대 70개의 랙과 210톤까지의 원자재를 보관할 수 있는 역량을 갖췄다. 이를 통해 다품종 소량 생산 환경에서 24시간 생산 자동화를 실현한다.
LiftMaster Compact는 적재과 하역을 동시에 수행하는 ‘싱크론 로더’ 기능을 탑재했다. 생산 프로세스를 단순화하고, 운용 및 인력 운영 비용 절감에 기여한다.
또 다른 선택지를 제공하는 TruBend Center 7020은 작업자 접근성이나 재료 적재·하역에 유연성을 높이도록 설계된 ‘개방형 장비 콘셉트’로 디자인됐다. 작업자가 측면에서 쉽게 적재·하역할 수 있고, 특히 4m/s 속도의 회전 매니퓰레이터를 통해 빠르고 정밀한 절곡을 지원한다.
주지훈 프로는 “현장 내 숨겨진 비효율을 잡아야 진정한 생산성을 확보할 수 있다”며 “자사는 장비, 소프트웨어, 디지털 기반 서비스를 유기적으로 통합한 ‘토털 솔루션 공급자’로서의 경쟁력을 강화하고 있다”고 강조했다.
TRUMPF는 이 일환으로, 클라우드 기반 예지보전 서비스로 장비 이상 징후를 사전에 감지하고, 이를 기반으로 한 선제적 서비스를 제공한다. 또한 AI 이미지 인식 기술 기반 분류 시스템 ‘Sort Master Vision’을 통해, 숙련도와 관계없이 절단 품질을 개선하고 작업 효율을 높이고 있다.
여기에 사무실 인력이 자신의 업무에 집중하도록 생애주기 최적화를 추구한다. 수요 예측, 자재 조달, 설비 및 인력 배정, 공정 흐름 설계 등을 포괄하는 기능을 각 장비·솔루션에 내재화했다. 이를 위해 ‘스마트 팩토리팀’과 ‘테크니컬 세일즈 팀’을 신설해 고객 맞춤형 자동화 구현에 총력을 기울이고 있다.
또한 현장에 여러 장비가 있을 때, 생산 계획을 분석한 후 최적화하는 ‘생산 계획 수립’ 기능도 함께 제공한다.
아울러 TRUMPF는 지속가능성 측면에서도 트렌드에 발맞추고 있다. 미절단 가공이 발생했을 때, 이를 즉시 인식하고 재절단해 예기치 않은 생산 중단 시간을 최소화하는 ‘스마트 리런(Smart Rerun)’, 자재를 조밀하게 배열해 낭비를 극소화하는 ‘나노조인트(Nanojoint)’ 등을 통해 불량률 감소와 폐기물 최소화를 도모하고 있다. 또 장비에 에너지 효율적인 노즐을 사용해 가스 소모를 줄이고, 노즐 자동 교체 기능으로 생산 중단을 최소화하는 등 친환경적이고 효율적인 생산 환경 조성에 힘쓰는 중이다.
더불어 사용자 서비스 영역에 DX를 이식하는 작업도 진행하고 있다. 모바일 서비스 애플리케이션 ‘마이트럼프(myTRUMPF)’ 및 ‘서비스 앱(Service App)’은 서비스 접점 디지털화를 통해 사용자에게 다양한 서비스를 제공한다.
사용자는 이 앱을 통해 장비 상태를 간편하게 확인하고, 고장 발생 시 에러코드를 기반으로 빠른 해결 방안을 제공받을 수 있다. 현재 전체 서비스 문의 중 80% 이상이 해당 앱을 통해 접수되고 있다.
주지훈 프로는 “장비와 서비스 양측면 모두 디지털화를 통해 고객 생산성을 극대화하는 것이 우리의 핵심 전략”이라고 밝혔다.
오토메이션월드 최재규 기자 |